Den frågan får vi på Qestio allt oftare av våra kunder. Mitt svar är att det finns ett antal faktorer som behöver finnas på plats innan man tar hjälp av exempelvis AI. Det finns oftast oerhört mycket effektivitetsökning att hämta hem genom att jobba med att utveckla processer och arbetssätt, innan Industri 4.0 eller AI gör nytta.
Nummer ett är alltid att säkerställa att underhållsprocessen är funktionell när det gäller planeringen och själva utförandet av underhållsåtgärderna. En annan åtgärd som gör mycket stor nytta för effektiviteten är att utveckla samarbetet mellan drift och underhåll. Ytterligare effektivitetshöjande åtgärder är att löpande mäta anläggningens tillgänglighet och underhållets effektivitet. Se slutligen till att införa ett kontinuerligt förbättringsarbete för driftstörningar och underhållsplaner.
Först när allt detta finns på plats och fungerar kan det vara en bra idé att utvärdera om och hur man kan dra nytta av Industri 4.0 och AI. Sanningen är den att om inte processen flyter och om inte underhållsarbetet fungerar kommer den nya tekniken inte bidra. Tvärtom så kommer tid och resurser att läggas på sådant som inte får någon särskild effekt. Den tiden och de resurserna tas oftast från det ”vanliga” underhållsarbetet.
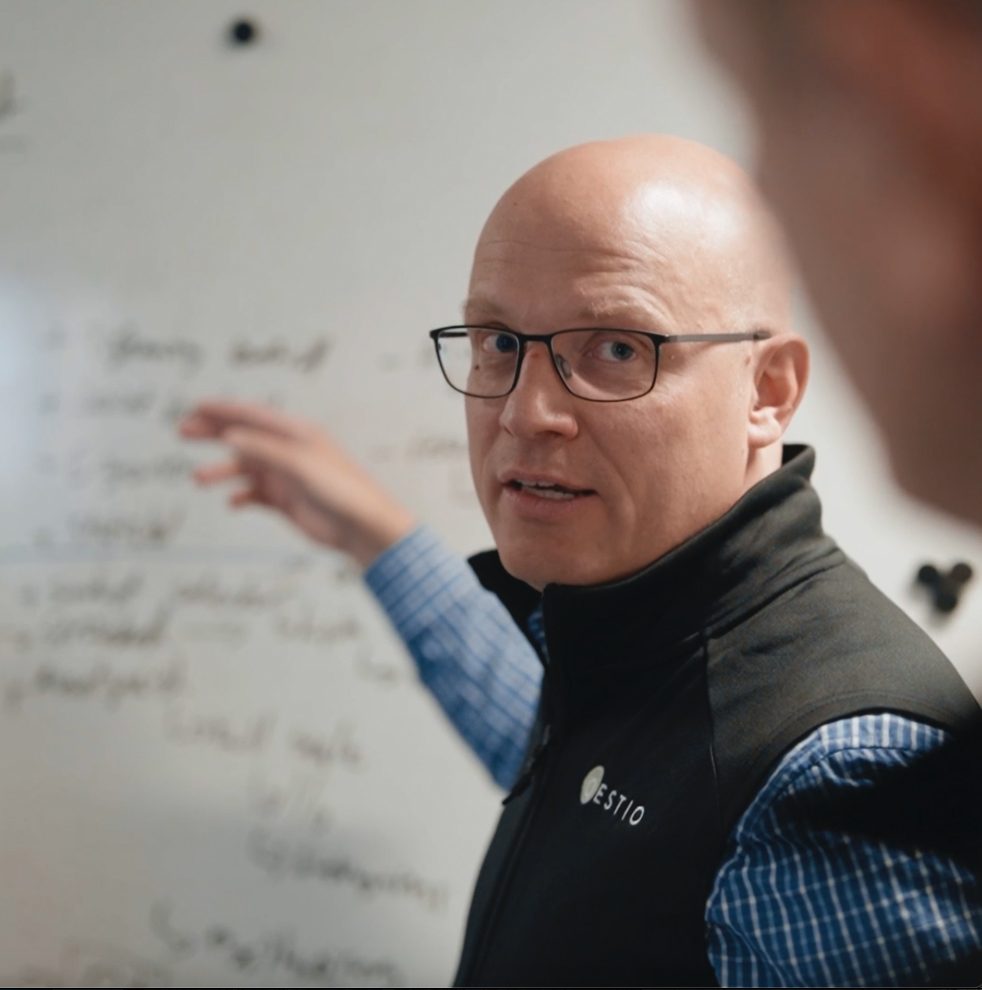
Det finns idag Big Data-analysverktyg inom underhållsområdet. Utvecklingen går framåt, men många tekniska applikationer i industrin är unika vilket gör att AI-modellen måste tränas. Det tar tid och resurser. I många produktionsverksamheter kan olika verksamhetsdelar bedrivas i olika utvecklingsnivåer, beroende på behovet kan det vara berättigat. I samma fabrik kan man använda både Industri 1.0 och industri 4.0. Att nyttja mätvärdesinsamling online (Industri 4.0) har använts inom underhåll sedan åtminstone 1980-talet. Med ny teknik har det blivit enklare och billigare. För att den data som samlas in ska ha ett underhållstekniskt värde behöver en viss struktur finnas på plats.
Den data man tar ut och loggar behöver analyseras med kunskap utifrån vilka värden som är relevanta. ”– Vad säger värdet om komponentens tekniska status?” ”– Hur påverkas utrustningens tillgänglighet om värdena förändras?” Utifrån analysen behöver sedan åtgärder vidtas. Det kan exempelvis vara att utvärdera felet vidare för att planera förebyggande åtgärd eller avhjälpande åtgärd. Om det inte finns en process för det här, saknar den insamlade datan ett verkligt värde.
Har ni bra koll på ert underhåll? Mäter ni och följer upp er tillgänglighet? Agerar ni utifrån uppföljningen? Reviderar ni era underhållsplaner löpande? Då kan ni fundera på nästa steg. En fingervisning kan vara att ha några nyckeltal på plats först.
- Teknisk tillgänglighet på mer än 80%
- Mer än 70% av underhållet är planerat
- En definierad beredningsprocess är på plats
- Mer än 90% av de planerade arbetena är beredda
- En struktur för mätning av effektiviteten i underhållets utförandeprocess.
Min erfarenhet är att det är väldigt få produktionsanläggningar i svensk industri som uppnår de här nyckeltalen löpande. De verksamheter som inte uppnår nyckeltalen har stor nytta av att fokusera på att utveckla sina processer och arbetssätt. Det kommer att betala sig med mycket högre ROI än exempelvis investering i ny mätteknik och datamodeller. Att fokusera på processerna tar produktionen 80% av vägen till vad brukar definieras som ”Underhåll i Världsklass”.