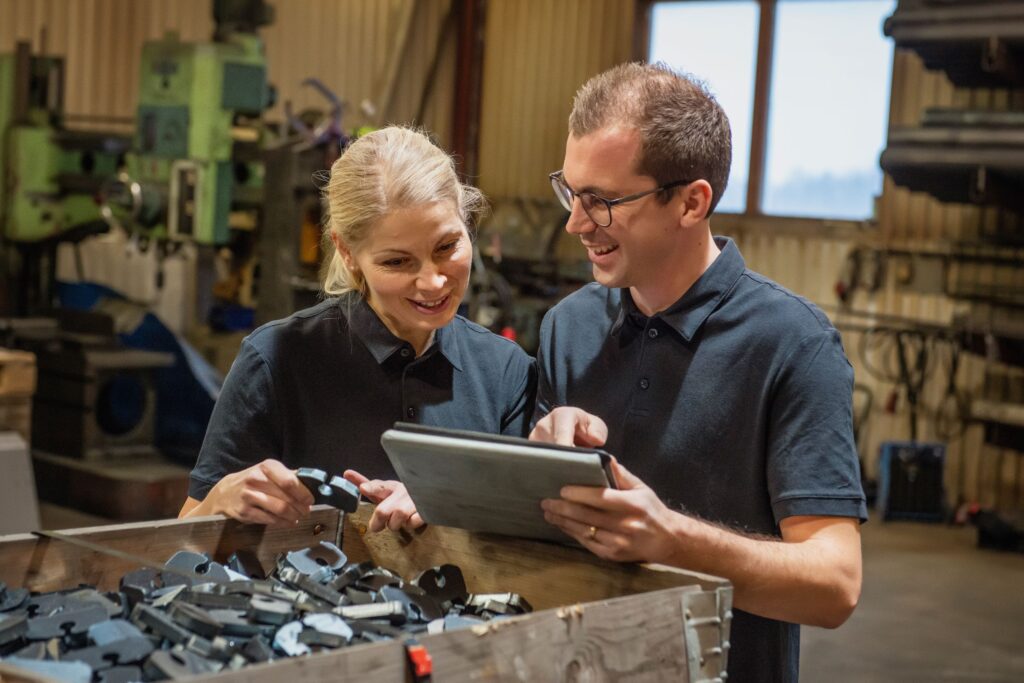
För att nå en effektiv produktion krävs utöver en god driftsäkerhet och stabil kvalitet på insatsmaterial ett effektivt arbetssätt som alla följer. Vad är det, hur uppnår man detta, hur utarbetar med det?
I Japanska företag efter andra världskriget utvecklades standardiserat arbete som en grundpelare i Lean production, t.ex. Datsun, Toyota, Yamaha, Sanyo, Mitsubishi. Under många år blev det utvecklat till en företagskultur som sedan under och efter 70-talet kallades ”det japanska undret” när deras produkter utklassade allt annat i världen. Det många inte känner till är att japanerna fick omfattande stöd och utbildning efter kriget av de som drev den amerikanska krigsindustrin till toppnivå, med hjälp av bland annat TWI (Training Within Industry) vilket är grunden till standardiserat arbete.
Genom att gemensamt utarbeta bästa kända arbetssätt tillvara tar man alla medarbetares kompetens, man skapar delaktighet och men ger förutsättningar för en bra implementering. Standardiserat arbete är inte arbetsinstruktioner som utvecklats av ingenjörer, fokuserade på standardeffektivitet och oflexibla på grund av koppling till kostnadsredovisning och produktkalkyl.
Den primära idén med standardiserat arbete är att det är en överenskommelse mellan ledare och de som utför uppgiften vanligtvis operatörer, men de kan också vara kundservicespecialister, HR-personal, ingenjörer, etc. som utvecklats genom ett samarbete. Det är inte något som vissa människor utvecklar, sedan ”distribuerar” det till dem som gör jobbet.
Standardiserat arbete eller bästa kända arbetssättet är det säkraste, enklaste och mest förlustfria sättet att göra ett jobb som vi för närvarande känner till. Den utvecklas och ägs av operatörer, teamledare och arbetsledare som arbetar tillsammans. Det ger en bas för framtida förbättringar. Det är mycket flexibelt, kan förändras genom Kaizen (förändring till det bättre) och möta taktiden eftersom den kan förändras. Det fungerar smartare – inte svårare eller snabbare.